2007荣格技术创新奖(金属加工业)历时4个月,在评审团、顾问、编委等多方共同努力下终于圆满完成。技术的进步离不开创新,此次活动的主旨是选出那些在过去一年中对金属加工业的进步和发展起了重要作用的技术。它们同时也是未来技术的趋势和走向。在评选过程中,我们发现了很多优秀的技术和产品,它们是工程师、工艺师和一线技术人员智慧的浓缩。对加工过程的改善和促进起了重要的作用,从而使加工能力和生产效率得到大幅提高、加工环境得到改善并且创造了巨大的经济效益。这些技术从概念到实践到成熟,最后在市场上广泛采用,其间需要克服来自多方面的困难、压力,需要付出辛勤的劳动,而执着的坚持并完成它们的企业和组织也担负了巨大的风险。在此,我们衷心的感谢那些对金属加工业技术的推动和发展做出了或大或小贡献的所有业内人士。以下是本届获奖的技术介绍,与读者共勉。 1. 多主轴加工技术 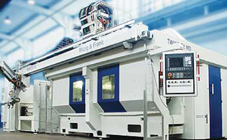 | Witzig&Frank公司的四主轴双工位加工中心Tiwinflex MD | 开发多主轴加工中心旨在利用多个主轴的同时或平行加工以提高机床的生产率。早在90年代中期,德国的Fritz Werner、Honsberg Lamb、Alfing Kessler和Ex-Cell-O等机床制造公司都开发出高速双主轴加工中心。在Y轴和Z轴上的两个主轴各自有自己的进给驱动装置,其工作彼此可以独立进行。当一个主轴进行加工时,另一个主轴则进行换刀。显著地提高机床的生产率。与单轴加工中心相比较,当时双主轴加工中心的价格仅高出20%(在目前,视机床装备的扩充情况,双主轴机床的价格一般要高出25~40%,作业面积大30%)。然而在加工的产量上可提高一倍,可显著降低工件的单件费用。 多主轴加工中心无论结构还是性能上均有很大的发展和提高。在集成的主轴数上,除了双主轴外,还有了三主轴和四主轴的加工中心;在坐标轴的数量上,除了三坐标外,有了五坐标多主轴加工中心。并且,在现代的多主轴加工中心上有的还采用了直线电机来直接驱动坐标轴的运动和采用转矩电机直接驱动安装夹具的回转支架进行回转摆动,从而大大提高了多主轴加工中心的动态性能和加工精度。而采用五坐标多主轴加工中心,不仅能大大提高生产效率,而且可实现工件在一次装夹下进行综合加工,从而进一步提高了加工精度。 在几年前,一些零件的加工,如轴承盖、泵体、转向节和ABS控制箱、油底盘、变速箱体和差速器壳等,大多数仍是采用单主轴加工中心进行综合加工,往往需要采用多台机床才能达到中、大批量生产所要求的产量。如果采用双主轴和四主轴加工中心,不仅减少了机床的外围设备(如排屑装置、换刀装置和托板交换装置等)和作业面积,还能够有效提高生产率。 5轴多主轴加工中心,可以实现多个工件在一次装夹下的五面综合加工,有效提高多主轴加工中心的生产率。因此多主轴加工中心属于高效加工设备,应用于中、大批量工件的加工,提高机床的可靠性和利用率十分重要。因此,对于机床用户来说,在加工计划的安排、零件加工程序的编制、刀具选用和机床的合理维护要给予特别的重视。 不少机床厂家推出了众多具有不同特色和应用范围的高速多主轴加工中心。如Cross Huller公司的“Specht 550 duo”:高速双主轴加工中心,机床采用“框中框”结构,主轴最高转速16000r/min,机床为3轴基本配置,作为选项,机床可扩充为5轴双主轴加工中心(即增加回转桥式支架并在其上面配置回转工作台)以便实现工件五面综合加工。Heller公司的“MCT160”: 在双主轴加工中心上配备有安装两个回转工作台的回转桥式支架,可进行工件的五面综合加工,并适合于进行干式加工或微量润滑。Alfing Kessle公司的“AL204”:系四主轴加工中心,相邻主轴间的距离仅为200mm,适合于小尺寸零件的批量生产,机床采用直线电机驱动,具有很高的动态性能。轴加速度达20m/s2,轴速度180m/min,主轴最高转速16000r/min,通过NC回转夹盘在2秒内可实现工件变换。(SW)施韦比施公司“BAW06-22”:双主轴加工中心,两主轴间距为600mm,适合于加工轻金属、大尺寸零件,主轴驱动采用同步电动机,这种5轴结构的加工中心可实现工件在任意角度下的五面综合加工。Witzig&Frank公司的“Tiwinflex MD”: 是一种四主轴双工位加工中心,在两个相互独立的加工模块上各装两个电主轴。可以实现与基本时间平行的上、下料,在仅3秒的时间内回转180°,使两个桥式夹具摆入或摆出加工区,工件可在加工区以任意的角度位置进行定位和加工。德国科恩(KERN)公司的超高速精密五轴加工中心“Kern Pyramid Nano” 是世界上第一台纳米级精度加工中心,采用专利的ARMORITH床身;采用流体静力(Hydrostatic)驱动及导轨系统,定位精度 ;Ps +/-0.3微米(VDI/DGQ3441);加工粗糙度可达Ra0.05微米 ;主轴转速最高可达160,000rpm。 此外还有DMG较新推出的Ultrasonic70是专门针对玻璃、陶瓷、硬质合金等先进材料(脆硬材料)的超声振动加工中心;TORNOS开发的多轴加工中心;北京机电院的VS1250是我国自主研发的第一台由直线电机驱动的高速立式加工中心 ;瑞士阿奇夏米尔集团HPM1150U立卧转换、5轴联动高速加工中心;哈挺的超精密车削中心SR 51 MSY和XR760加工中心;德国贝托特哈默机械制造有限公司的高速高精度加工中心、铣床等。 2. 复合机床加工技术 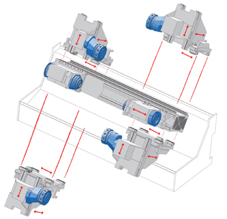 | Traub公司复合机床的模块化系统 | 近十年来,由于控制技术和驱动技术的长足进步,推动了车床向多功能机床方向发展。在本世纪初,机床复合化发展迅速,众多机床制造厂家推出了具有不同结构和特色的车铣、车钻铣和车磨中心等各种复合机床。 通过在一台机床上集成多种不同的加工工艺实现工件尽可能在一次装夹下的综合加工。 在加工工艺的集成上,是根据机床设定的适用范围,有选择地来集成车、钻、铣、滚齿、磨削以及激光焊接、淬火和切割等工艺,配备相应的主轴和加工部件。如车铣中心,一般均配备有工件轴(主轴)、背主轴和转塔刀架等,工件轴除实现高速旋转外,还能进行回转分度。而在转塔刀架上装有固定式刀具和驱动式刀具。复合机床的调整则是通过NC程序来实现的,因而具有较高的加工柔性。因此,这类复合机床特别适合于工件投产批量较少而品种又多的中小企业使用,也适合用于中大批量回转体零件的加工。 复合机床主要是针对回转体复杂零件的综合加工而开发的一种多工艺机床,对于回转体零件,主要的加工工序是车削,其次是铣削、钻削和磨削。因此,有相当数量的复合机床,将车、铣工艺进行复合,构成车铣中心。也有不少复合机床将车削、铣削和磨削进行复合,形成车磨中心,用来进行零件的硬加工。 车、磨两种工艺的复合其优点在于:加工表面粗糙度Rz<4μm和公差等级<IT5的功能表面可通过磨削来实现,而工件在同一装夹下的硬车,不仅可用来减少磨削余量,降低磨削的基本时间,而且使磨削加工工艺成为纯粹是产生光洁表面的加工工艺。 值得一提的是,像EMAG和Weisser Sohne等公司的车磨复合机床上均可实现干式磨削加工。这类机床完全可进行干式加工。目前,在正确选择CBN砂轮的晶粒、强度、破损特性和粘结剂的情况下,干式磨削速度可达到80m/s。 复合机床普遍遵循模块化设计原则来构建,通过机床的模块化结构,不仅易于集成多种不同的加工工艺,而且能针对用户的加工任务提供最佳的加工方案和最合理的机床配置。像Ex-Cell-O、Index和Traub等公司的复合机床均采用模块化结构,可以为用户提供量体裁衣的解决方案。 在一次装夹下实现工件的综合加工,是简化生产工艺流程、提高加工精度和降低产品制造成本的重要途径。 3. 激光切割技术 世界第一台CO2激光切割机是二十世纪七十年代的诞生的。三十多年来,由于应用领域的不断扩大,CO2激光切割机不断改进,目前国际国内已有多家企业从事生产各种CO2激光切割机以满足市场的需求,有二维平板切割机、三维空间曲线切割机、管子切割机等。激光的应用领域也在不断扩大:采用三维激光切割系统或配置工业机器人,切割空间曲线,开发各种三维切割软件,以加快从画图到切割零件的过程;为了提高生产效率,研究开发各种专用切割系统,材料输送系统,直线电机驱动系统等,目前切割系统的切割速度已超过100m/min ;大功率的激光切割技术使切割低碳钢厚度已超过30mm,并特别注意研究用氮气切割低碳钢的工艺技术,以提高切割厚板的切口质量。 在激光切割技术领先的国外知名企业有德国Trumpf公司、意大利Prima公司、瑞士Bystronic公司、日本Amada公司、MAZAK公司、NTC公司、澳大利亚HG Laser Lab公司等。目前国内能提供平板切割机的企业有上海团结普瑞玛公司、沈阳普瑞玛公司、济南捷迈公司、武汉楚天公司,深圳市大族激光科技股份有限公司等。 4. 高速加工和电火花成型联合技术 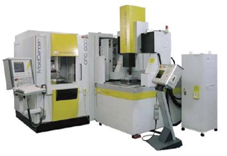 | OPS-Ingersoll的模具中心 | 高速加工和电火花成型机联合技术——模具中心,将两台电火花成型机或一台高速铣削加工中心和一台电火花成型使用智能机器人联合起来,成为自动化的模具制造中心。该模具中心综合了五轴高速铣削、电火花成型、自动化等多项尖端技术。在模具中心电极和模具是全自动生产的。搬运系统会自动识别和装夹电极。 在高速铣削中心上加工电极的同时,可在电火花机上放电加工另一个模具,操作单元自动管理和操作工作台和电极。电火花成型机通过机器人搬运单元自动调入电极,自动放电加工模具。在一个完整的生产线上完成从CAD/CAM制图到模具准备——读取IGES文件数据,编制CAM铣削程序,输出放电加工要求,EDM-数据传输到电火花成型机。电火花成型机通过机器人搬运单元自动调入电极,自动放电加工模具。与传统加工相比,通过使用高速铣和电火花联合技术能够提高产品质量,较大程度减少手工去毛刺,减少50%以上的加工时间,通过自动化有效提高车间效率,通过使用石墨电极和高速加工降低成本。目前能够提供该项技术的仅有OPS-Ingersoll公司。 5. 精密电火花加工技术 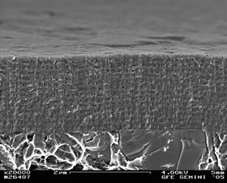 | 1943年,原苏联的科学家拉扎连柯夫妇将电蚀变为电火花加工,成为特种加工手段,已有半 个多世纪,它的发展速度是惊人的,现已发展成为在某些场合不可替代的的加工手段,且已 具有超精密加工的能力。 目前,电火花加工主要的有两种,即电火花线切割和电火花成型加工。成型型腔电火花加工的表面粗糙度已可达到镜面。电火花线切割的精度已可以达到±2 ~3μm,而其切割的缝隙仅为电极丝粗细;从其功能发展来看,是一 般机械加工很难做到的,如劈锥、挠性接头、级进模等。且电火花线切割机床,从诞生的时候,就和计算机数控技术结合在一起,这为实现自动化奠定了基础。 微机械的出现,使电加工开始向小型化突破,如喷丝头的成型小孔采用反拷法在电火花成型机上进行加工 ;为了加工小型电机或微型齿轮等微小型零部件,在电加工领域便出现了一种采用直径0.01mm钨丝的微小型电火花线切割机。 电火花加工技术的代表性企业及产品有阿奇夏米尔的AGIECUT PROGRESS V2当今世界上加工效率最高的慢走丝线切割机床,较大切割效率>500 mm2/min,丝径范围:0.07 -0.33 mm,最佳表面粗糙度Ra < 0.2 um。 德国的Vollmer Werke Maschinenfabrik GmbH公司的QWD755/760系列五轴卧式CNC线切割加工机床,可对阶梯刀具、成型加工刀具以及其它复杂形状刀具进行连续走丝成型加工。第五轴(E轴)上的电极丝采用水平位置安装,克服了传统线切割机床电极丝垂直安装造成工件轮廓加工困难的缺陷,可获得≤Ra0.2μm 的加工表面粗糙度。 6. CAM技术 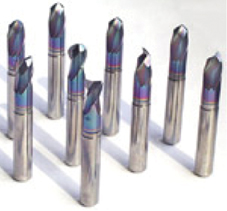 | 20世纪60年代在专业系统上开发的编程机及部分编程软件如 :FANOC、Semems编程机,系统结构为专机形式,基本处理方式是人工或辅助式直接计算数控刀路,编程目标与对象也是数控刀路。其后CAD/CAM集成系统较好地利用了CAD模型,以几何信息作为最终的结果,自动生成加工刀路。自动化、智能化程度得到了大幅度提高,具有代表性的是UG、DUCT、Cimatron、MarsterCAM等。基本特点是面向局部曲面的加工方式,表现为编程的难易程度与零件的复杂程度直接相关,而与产品的工艺特征、工艺复杂程度等没有直接相关关系。 现在CAM面向整体模型(实体)、工艺特征。系统将能够按照工艺要求(CAPP要求)自动识别并提取所有的工艺特征及具有特定工艺特征的区域,使CAD/CAPP/CAM的集成化、一体化、自动化、智能化成为可能。新一代CAM系统不仅可智能化判断工艺特征,而且具有模型对比、残余模型分析与判断功能,使刀具路径更优化,效率更高。同时面向整体模型的形式也具有对工件包括夹具的防过切、防碰撞修理功能,提高操作的安全性,更符合高速加工的工艺要求,并开放工艺相关联的工艺库、知识库、材料库和刀具库,使工艺知识积累、学习、运用成为可能。 大型CAD软件的一体化CAM模块,如UG、CATIA等,其编程功能强大,但要用好也有一定的难度;还有一类是CAD功能相对较弱而CAM模块比较出名的中型软件,主要特点是功能实用又相对较容易掌握,可谓高手新手都能用的,如Delcam 公司的PowerMILL及WorkNC采用面向工艺特征的处理方式,系统以工艺特征提取的自动化来实现CAM编程的自动化。当模型发生变化后,只要按原来的工艺路线重新计算,即实现CAM的自动修改。由计算机自动进行工艺特征与工艺区域的重新判断并全自动处理,使相关性编程成为可能。目前已有成熟的产品上市,并为北美、欧洲等发达国家的工模具界所接受。Pathtrace工程系统公司的EdgeCAM系统是针对三维实体特征进行加工 ; Cimatron推出的CimatronE微铣削软件。 微铣削(Micro-milling)是加工微小零件和高精密零件的一种全新加工技术。微铣削使用非常小的刀具(直径小于0.1mm)并能获得非常小的曲面公差和高质量的曲面精度。 7. CAD特征造型技术 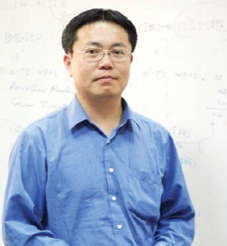 | CAD技术从二维绘图起步,经历了三维线框、曲面和实体造型发展阶段,注重于描述产品的几何信息;而特征造型则是着眼于更好地表达产品完整的功能和生产管理信息,为建立产品的集成信息模型服务。特征(feature)在这里作为一个专业术语,兼有形状和功能两种属性,它包括产品的特定几何形状、拓扑关系、典型功能、绘图表示方法、制造技术和公差要求。特征造型技术使得产品的设计工作在更高的层次上进行,设计人员的操作对象不再是原始的线条和体素,而是产品的功能要素。特征的引用直接体现了设计意图,使得建立的产品模型更容易为人理解和组织生产,为开发新一代的基于统一产品信息模型的CAD/CAPP/CAM集成系统创造了前提。 美国EDS公司的UG产品采用基于特征的实体造型。UG是集CAD、CAE和CAM于一体的机械工程辅助系统。具有尺寸驱动编辑功能和统一的数据库,实现了CAD、CAE、CAM之间无数据交换的自由切换,具有很强的数控加工能力,可以进行2轴~2.5轴、3轴~5轴联动的复杂曲面加工和镗铣。UG还提供了二次开发工具GRIP、UFUNG、ITK,允许用户扩展UG的功能。 美国SolidWorks公司的产品是采用基于特征的实体建模,参数化设计具有可修改性。该软件采用自顶向下的设计方法,可动态模拟装配过程,先进的特征树结构使操作更加简便和直观。较新推出的SolidWorks 2007软件的智能特性技术“SWIFT” 能自动以设计师所需的正确顺序生成新的特征,使3D CAD 跨越了从自动化到智能化的门槛。 8. CAD参数化造型技术 参数化实体造型方法。主要的特点是 :基于特征、全尺寸约束、全数据相关、尺寸驱动设计修改。 全尺寸约束,即设计者在设计的全过程中,必须将形状和尺寸联合起来考虑,并且通过尺寸约束来控制形状,通过尺寸的改变来驱动形状的改变,一切以尺寸为出发点。 美国Parametric Technology Corporation公司(简称PTC)的Pro/Engineer系统是基于约束的参数化造型模块。以其先进的参数化设计、基于特征设计的实体造型而深受用户的欢迎。Pro/Engineer建立在工作站上,使系统独立于硬件,便于移植;该系统用户界面简洁,概念清晰,符合工程人员的设计思想与习惯。Pro/Engineer整个系统建立在统一的数据库上,具有完整而统一的模型,能将整个设计至生产过程集成在一起,共有20多个模块可供选择。 法国达索(Dassault)飞机公司的CATIA是采用参数化技术的系统。CATIA系统是集成化的CAD/CAE/CAM系统,具有统一的用户界面、数据管理以及兼容的数据库和应用程序接口,并拥有20多个独立模块。美国波音飞机公司的波音777飞机便是其杰作之一。 9. CAD变量化设计技术 CAD技术起步于50年代后期,随着计算机软硬件技术和计算机图形学技术的发展而迅速成长起来。 CAD在机械制造行业的应用最早,也最为广泛。世界各大航空、航天及汽车等制造业巨头不但广泛采用CAD/CAM技术进行产品设计,而且投入大量的人力物力及资金进行CAD/CAM软件的开发,以保持自己技术上的领先地位和国际市场上的优势。 当所设计的零件形状过于复杂时,面对满屏幕的尺寸,如何改变这些尺寸以达到所需要的形状就很不直观;再者,如在设计中关键形体的拓扑关系发生改变,失去了某些约束的几何特征也会造成系统数据混乱。 变量化设计(Variationaldesign)是指设计对象的修改需要更大的自由度,通过求解一组约束方程来确定产品的尺寸和形状。约束方程可以是几何关系,也可以是工程计算条件,设计结果的修改受到约束方程驱动。变量化设计允许尺寸欠约束的存在,这样设计者便可以采用先形状后尺寸的设计方式,将满足设计要求的几何形状放在第一位而暂不用考虑尺寸细节,设计过程相对宽松。变量化设计可以用于公差分析、运动机构协调、设计优化、初步方案设计选型等,尤其在做概念设计时更显得得心应手。 变量化技术既保持了参数化技术的原有的优点,同时又克服了它的许多不利之处。它的成功应用,为CAD技术的发展提供了更大的空间和机遇。 众所周知,已知全参数的方程组去顺序求解比较容易。但在欠约束的情况下,其方程联立求解的数学处理和在软件实现上的难度是可想而知的。美国SDRC(Structural Dynamics Research Corporation)公司攻克了这些难题,并就此形成了一整套独特的变量化造型理论及软件开发方法,I-DEAS Master Series软件系列。以其高度一体化、功能强大、易学易用等特点而著称。其较大的突破在于VGX技术(Variational Geometry Extended),极大地改进了交互操作的直观性和可靠性。另外还增强了复杂零件设计、高级曲面造型以及有限元建模和耐用性分析等模块的功能。在中国,正式使用I-DEASMasterSeries软件的用户已经超过400家。 开目CAD是华中理工大学机械学院开发的具有自主版权的基于微机平台的CAD和图纸管理软件。开目CAD支持多种几何约束种类及多视图同时驱动,具有局部参数化的功能,能够处理设计中的过约束和欠约束的情况。开目CAD实现了CAD、CAPP、CAM的集成。 10. 有限元分析软件技术 CAE的理论基础起源于1943年数学家Courant尝试用定义在三角形区域上的分片连续函数的最小位能原理来求解t.Venant扭转问题。 20世纪80年代结构优化设计开始应用于工程优化设计中,发展成专业的工程优化设计软件。有限元分析技术在结构分析和场分析领域获得成功后,逐步从力学模型拓展到各类物理场的分析;从线性分析向非线性分析发展,从单一场的分析向几个场的耦合分析发展。出现了许多著名的分析软件如Nastran,I-DEAS,ANSYS,ADINA,SAP系列等。借助于CAE计算分析指导产品结构中某些部分进行修改,以期得到更加优良的性能;对新开发的产品进行仿真分析,验证预期的功能,及时发现设计中的缺陷,使新产品更加有效、可靠。 结构强度与寿命评估变得越来越复杂,需要借助于相关的理论、方法、行业规范以及材料数据,这些都是经过大量实验、工程实践总结归纳出来的,将这方面的科研成果编制成软件。如MSC.FAUIGUE软件、MSC.MARC软件中的失效与破坏分析模块。在CAD造型设计的基础上形成了工程结构的动态仿真,在这方面已推出的软件有ADAMS和WorkingModel等,它们是通用的机械结构仿真软件。ADAMS提供了模拟实际系统运动和动力过程的仿真环境,可以全面地仿真实际制造活动中的结构、信息及制造过程。 世界三大有限元分析软件公司MSC、ANSYS和SDRC。MSC和ANSYS专注于非线性分析市场,SDRC则更偏向于线性分析市场,同时SDRC发展起了自己的CAD/CAE/PDM技术。除此之外许多新的CAE软件发展迅速。如MARC公司致力于发展用于高级工程分析的通用有限元程序,程序重点处理非线性结构和热应力问题。 11. 数字化精密测量技术 数字化精密测量技术是数字化制造技术中的关键技术之一。开发亚微米、纳米级高精度测量仪器,提高环境适应能力,增强鲁棒性,使精密测量装备进入生产现场,集成到加工机床和制造系统,形成先进的数字化闭环制造系统,是当今精密测量技术的发展趋势。 美国FARO技术公司的FaroARM系列便携式三坐标测量臂在工业界首次实现测量臂与激光扫描头的结合,在同一坐标系下实现非接触式快速扫描和接触式测量。特点:非接触式灵活快速扫描,获取曲线曲面的点云数据,点云无分层;接触式测量,把握关键特征尺寸与轮廓的精度。提高了准确性,做产品检验时用户通常通过5到10个点来定义曲面,使得用户可以检验由数以万计的点云定义的曲面质量;自动化的SPC可对多个样品进行自动化的统计过程控制 。 美国CIMCORE公司推出了配备有先进激光扫描测量系统的关节臂测量机。材料采用碳纤维,INFINITE系列还具有无线通讯功能。实现测量过程的实时显示和补漏测量数据的无缝拼接。 数控机床的精度和性能检测领域中,国外著名厂商Renishaw、API及HP等公司生产的激光干涉仪测量系统和球杆仪等在数控机床的几何精度和运动精度的检测和监控中,无论在机床制造厂还是机床使用厂,都得到了广泛的应用。Renishaw公司的激光干涉测量系统,配备了高精度、高灵敏度的温度、气压、湿度传感器及EC10环境补偿装置,在工作环境下测量精度得到进一步提高;API公司的Rmtea六维激光测量系统可同时测量6个数控机床精度项目的误差,缩短了检测时间,为生产现场数控机床的检测和诊断提供了更为快速高效的精密测量手段。 12. 水溶性切削液 切削液是金属切削加工的重要配套材料。最早人们采用动植物油作为切削液,但动植物油易变质,使用周期短。20世纪初,人们发明了各种润滑添加剂,在第一次世界大战后,开始研究和使用矿物油和动植物油合成的复合油。 刀具材料的发展推动了切削液的发展。随着切削温度的不断提高,油基切削液的冷却开始无法完全满足切削要求,此时人们开始重新重视水基切削液的优点。1915年生产出水包油型乳化液,并于1920年成为优先选用的切削液用于重切削。1948年在美国研制出第一种无油合成切削液,并在20世纪70年代由于油价冲击而使应用提高。 金属切削液通常可分为以冷却为主的水溶性金属切削液和以润滑为主的纯油性金属切削液;水溶性金属切削液则发展为可溶性油(乳化液)、半合成切削液和合成切削液三种。 水溶性切削液拥有一些相对于非水溶性切削液特有的优点:如可用于非水溶性切削液潜在发生火灾危险的场所;相比于非水溶性切削液,冷却效果更好; 不会引起机床周围的污染,从而保持操作环境的清洁 ;从价格上考虑,在适用范围内,水溶性切削液可大幅度降低切削液的成本。 以后的发展趋势将有希望以从水溶性切削液代替非水溶性切削液的应用,并朝向通用型的方向发展。其中,微乳化液因其优势,将成为未来的主要发展趋势。 目前,一些知名企业正在不断加大对水性切削液的研究和开发。如,嘉实多Alusol AZ 是一种专为铝和铝合金的机加工而研制出的高性能水溶性切削液。该产品不含氯,但它克服了铝加工中常见的诸如切削焊熔,工具磨损,表面光洁度差和生锈等问题,可适用于单机和中央冷却系统;米拉克龙推出的CS QS XLH新一代生物稳定半合成加工液,同样是此类产品的代表,它具有乳化液般的表现能力,总硬度达400ppm时混合物保持稳定;巴索国际贸易的切削液除了获得机床供应商DMG、GROB、HELLER、MIKRON、CHIRON、MORI SEIKI的好评外,在一些特殊行业如航空获得BOEING波音、AIR BUS空中客车等认可,电脑硬盘行业获得SEAGATE希捷认可等。 13. 环保型切削液添加剂 切削液性能的优劣、废液处理的难易、对操作者的危害和对环境的污染程度均取决于这些添加剂的种类及性能。作为未来的切削液添加剂,必须性能优良,对人体和环境无害。常用的亚硝酸盐及类似的化合物、磷酸盐类化合物、氯化合物、甲醛及类似的化合物都对人体和环境有害,应当加以限制。因此研究开发新型高效无毒添加剂,是生产环境友好性切削液的前提。在各方的关注下,已经有一些新型的添加剂成功投入使用: 1) 硼酸酷类添加剂 硼酸醋是一种多功能环保型添加剂。①硼酸醋的油膜强度高,摩擦系数低,具有优良的减摩抗磨性能;②具有良好的防锈性能 ;③具有抗菌和杀菌功能,且无毒害作用。 2) 钼酸盐系缓蚀剂 作为防锈剂是无毒的,也不污染环境,但它价格昂贵。 3) 新型防腐杀菌剂 近年来,由于环境保护法规的颁布和施行,许多国家都在限制使用有毒的防腐杀菌剂,研究开发新型防腐杀菌剂。美国Mobil化学公司研制出一种名叫Mobilment AquaRho的乳化油,添加了含磷、氮和硼的合成物,乳化液的使用寿命达4个月以上。 Exxon Mobil、Blaser、Castrol、Milacron、Quaker等业界知名切削液生产商将环保事业进行到底,巴斯夫、汽巴精化、克莱恩、罗门哈斯、德固赛等大型精细化工产品公司则为广大用户提供符合时代要求的环保添加剂。 14. 硬化膜沉积技术 硬化膜沉积技术最早即在工具(刀具、刃具、量具等)上应用,效果极佳,后用于模具、零部件和装饰产品等领域。目前CVD(化学气相沉积技术)和PVD(物理气相沉积技术)发展比较成熟。CVD技术出现于二十世纪六十年代,其涂覆温度多在1000℃以上,因此不适宜用于高速钢刀具的涂层。七十年代末,PVD(物理气相沉积技术)诞生。 PVD技术,是一种在高速钢和其它钢种刀具及其它工具表面涂敷耐高温、耐磨材料薄层的工艺方法。该法除可以对切削工具进行表面强化处理外,也可以对其它要求耐磨的机器零件,进行表面强化处理。CVD技术,是利用金属卤化物的蒸汽、氢气和其它化学成分,高温下,在加热基体表面形成固态沉积层的一种方法。是硬质合金刀片表面强化处理方法之一,已经成为一些国家标准化可转位刀片表面涂敷工艺。 新技术的发展方面,除综合了PVD和CVD的PACVD法外,还有MT-CVD(中温化学气相沉积)技术——克服了一般HD-CVD(高温化学气相沉积)的缺点;离子束溅射方法;中能离子束辅助沉积技术(IBAD);利用等离子体来促进化学反应的等离子辅助化学气相沉积(PCVD)——可使沉积温度降低到200~500℃。 精密加工应用领域的涂层最终用户往往会接触到各种各样不同的涂层。Sulzer (苏尔寿) Metaplas 开发出了纳米晶体Saturn涂层。该涂层具有优异的粘附性能、抗氧化性能和韧性以及表面硬度。在干式和微量润滑加工条件下更为卓越的红硬度。涂层技术的发展方向之一是通过添加硬质材料来提高其抗氧化性能和表面硬度。 该涂层为纳米多层结构,兼具高硬度(超过4500HV)及与被加工材料的低粘附倾向。除了硬质含铁材料的加工外,还可应用于有色金属和复合材料的切削加工。 目前,世界知名的涂层技术供应商都可以提供成熟而先进的硬化膜沉积技术,其中代表性的公司还有瑞士Oerlikon Balzers、瑞士SulzerMetco、瑞士Ionbond、英国Bodycote、瑞士Platit,德国CemeCon、德国PVT、德国Metaplas Ionon等。 15. 新型锻压技术 1842年,英国的内史密斯制成第一台蒸汽锤,使锻造进入应用动力的时代。以后陆续出现锻造水压机、电机驱动的夹板锤、空气锻锤和机械压力机。20世纪初期,随着汽车开始大量生产,热模锻迅速发展,成为锻造的主要工艺。20世纪中期,热模锻压力机、平锻机和无砧锻锤逐渐取代了普通锻锤,提高了生产率,减小了振动和噪声。 新型锻压机的发展趋向主要可以概括为:高自动化、成套化、成线化——锻压机的发展与汽车工业的发展密切相关,锻压机的发展趋向相当一部分满足了汽车覆盖件的生产要求,成套化成线化还带来了新的技术组合。 高柔性、复合化——复合了板材加工过程的不同工艺,满足了不同的生产要求。大型工位压力机是目前世界最先进高效的板材冲压设备,其特点是生产效率高,制件质量高,满足了汽车工业大批量生产对冲压设备的要求。此类产品还有如通快公司的数控砖塔冲床;意大利瓦尼尼公司为人熟知的P4多边折弯中心等。 高精、高效、高速度——高速压力机属于此类产品的代表。由于精密小型电子零件的需求增长,模具趋于小型化,生产要求更高效率。 环保、节能、降噪——环境友好是现今持续的主题,环保产品成为厂商的共识,一些公司纷纷研制出低噪声、低振动伺服压力机。如AIDA公司的一款伺服压力机甚至可以在无声模式进行运转。 新型锻压技术在技术实力雄厚的世界知名企业中得到最多开发应用,此类企业以德国Walter Scheid、日本丰田、日本本田、美国FinkT&sons锻造公司、德国Schuler、一汽巴勒特锻造(长春)有限公司等公司为代表。 16. 快速制造技术 快速制造(RM-rapid manufacturing)是基于离散-堆积成形原理的先进制造技术的总称。由产品的三维CAD模型数据直接驱动,组装(堆积)材料单元而完成任意复杂具有使用功能的零件的技术。直接快速制造可以避免繁复的工、模具制造;降低产品制造的耗时 ;使产品的制造成本有较大的下降。可增加产品设计的自由度,可采用非均质材料,可采用客户定制以及及时制造的生产方式,易于实行异地制造等。 激光立体光刻技术最早是由美国3D System公司开发,由计算机传来的三维实体数据文件,经软件分层处理后,驱动扫描激光头,发出紫外激光束在液态紫外光敏树脂的表层进行扫描。液态树脂表层受光束照射的那些点发生聚合反应形成固态。每一层的扫描完成之后,工作台下降一个凝固层的厚度,一层新的液态树脂又覆盖在已扫描过的层表面。利用这种快速成形工艺可以快速制造功能零件。生产SLA 系统的主要制造商有美国的3Dsystems公司、德国的EOS公司以及国内的西安交通大学等。 分层实体制造技术将特殊的箔材一层一层地堆叠起来,激光束只须扫描和切割每一层的边沿。常用的箔材是在一个面上涂热熔树脂胶的纸。箔材由供料卷筒被拉出,胶面朝下平整地经过造型平台,由位于另一方的收料卷筒收卷起来。每敷覆一层纸,就由一个热压辊压过纸的背面,将其粘合在平台上或前一层纸上。这时激光束开始沿着当前层的轮廓进行切割。激光束经准确聚焦,使之刚好能切穿一层纸的厚度。在模型四周和内腔的纸被激光束切割成细小的碎片以便后期处理时可以除去这些材料。LOM模型相当坚固,它可以进行机加工、打磨、抛光、绘制、加涂层等各种形式的加工。 生产LOM 系统的主要制造商有美国的Helysis公司、新加坡的KINERGY 公司、日本的KIRA公司以及国内的清华大学、华中科技大学等。 17. 金属直接熔敷/烧结技术 金属直接熔敷/烧结技术可称为激光粉末熔接或激光粉末淀积。采用高能激光,在基底表面,例如一个模具的表面,产生一个小的熔化池,同时一个汇聚的细磨金属颗粒流注入熔融池,以增加材料的体积。金属颗粒熔融并与基底金属接合,形成复合层。通过这样一层一层的迭加,模具可以填充成一个新的、接近最终的形状,这样就可以加工到最终的形状和公差。 这过程也能用来涂敷涂层和进行表面修整,免去传统涂层和电镀技术所固有的多孔性,而且涂层厚度或材料成分没有限制。自从二十世纪九十年代,在政府基金的支持下,许多学术研究所和研究实验室都巳对这过程作进一步的开发。通过技术转让,至少有两个公司巳经能基于这些研究,开发出商品化的系统。美国密歇根州Auburn Hills的POM Group, Inc.(www.pomgroup.com) 巳经商品化一种版本的技术,是密歇根大学开发的所谓直接金属淀积。POM的主要重点是工艺装备行业,他们的过程开发小组为用户提供先进的工艺装备、工艺装备重建和工艺装备重新组合,而他们的机器设计和制造组为满足特殊用户应用和行业需要,设计、制造和安装直接金属淀积系统。 POM巳经完成的工作的一个例子是涉及一个模具,这模具用于制造美国通用汽车公司要求的,在近期型号的汽车保险杠上增加卤素灯。POM能用它的直接金属淀积法,在老的保险杠模具上淀积新的材料,然后,把它加工到新形状,节省了通用公司制造一套新模具的成本。 另一家公司——密歇根州普利茅斯的Fraunhofer USA(www.ccl.fraunhofer.org) 也与密歇根州立大学合作,在用户工厂进行新产品、工艺和应用开发,包括设计和生产与试验系统的集成。Fraunhofer主要是工艺过程研究和开发实验室,但也进行生产。迄今,他们巳经发布了用于表面硬化的系统,但不是用于模具修理。 18. 高速和超高速磨削 磨削加工是一种具有悠久历史的加工方式,但磨削速度却始终处于低速水平。1929年,德国切削专家Carl.J.Salomon博士提出了“热沟”假设——在高速加工区,存在一个“热沟”,在“热沟”区,切削温度随加工温度急剧上升,直到温度达到最高点,之后伴随速度的提高,温度下降,该假设在后来的科学研究中得到证实。为高速和超高速磨削得发展指明了方向。 超高速磨削主要技术有: 快速点磨削——德国Junker公司1994年开发,继承了超高速磨削、CBN超硬磨料和CNC柔性加工三大先进技术,使超高速磨削技术在高效率、高柔性和大批量生产高质量稳定性方面的又一新发展,主要用于轴、盘类零件加工; 缓进给磨削——其特点是采用大的切削深度和很小的工件进给速度,通过大砂轮切深来增加磨削长度,以获得高磨除率,该方法在平面磨削中占主导地位,主要用于磨削沟槽和成型表面; 高效深磨——是一种集合了砂轮高速度、高进给度和大切深的高效率磨削技术,可以获得与普通磨削技术相近的表面粗糙度,而使材料磨除率比普通磨削高得多,德国Guhring Automation公司、日本三菱重工、美国Edgetrk Machine等都是知名的深磨机床生产商; 超高速精密磨削——砂轮速度的提高可以减小工件表面残留凸峰性变形的程度,从而有助于减少磨削表面粗糙度,该技术提高加工工件表面精度和质量; 以及砂带磨削——在材料表面经加工中有着“万能磨削”何“冷态磨削”之称的新型涂附磨削工艺。 高速与超高速磨削是提高磨削效率、降低工件表面粗糙度和提高工件加工质量的先进加工技术,尤其对硬脆材料也能实现延性域磨削,对高强度难磨削材料也能取得好的磨削效果。目前,实际应用的超高速磨削速度在200~250m/s。 19. 激光热处理技术 激光技术在本世纪60年代初诞生,激光热处理的试验研究起始于1979年,最初是在250W的小功率激光器上用小试样验证了钢表面相变硬化的效果。我国由铁科院金化所和中科院长春光机所等单位率先开展。目前,随着大功率激光器的发展,用激光就可以实现各种形式的表面处理。 激光热处理技术拥有显著优点:可无需使用外加材料;处理层和基体结合强度高,获得的组织细密、硬度高、耐磨性能好;被处理件变形极小,适合于高精度零件处理;可以进行局部选择性淬火,适合其它热处理方法无法胜任的表面处理;激光可以远距离传送,可以实现一台激光器多工作台同时使用,采用计算机编程实现对激光热处理工艺过程的控制和管理,实现生产过程的自动化。 激光热处理技术在汽车行业应用极为广泛。例如,美国通用汽车公司用十几台千瓦级CO2激光器,对换向器壳内壁局部硬化,日产3万套,提高工效四倍。模具的制造工艺复杂,形状各异,精度要求高,应用广泛,但模具的寿命短成本高,返修也很困难。用激光对模具表面进行热处理,已逐渐被认识和被采用,可成倍的提高模具的寿命,又不受形状和尺寸的限制。 武汉华工激光工程有限责任公司、武汉团结激光股份有限公司、楚天激光集团、富通集团、北京机床研究所激光热处理工程公司、武汉金石凯激光技术有限公司等都是典型的激光热处理设备供应商。 20. 热胀冷缩式刀夹 在机床主轴-夹头-刀具系统中,质量不对称(不平衡量)主要是由刀具的不对称形状、刀夹的不对称、主轴的圆跳动和磨损、系统构件的加工误差、冷却润滑液的影响等问题引起的。热胀冷缩式刀夹诞生于20世纪中期,该系统对高速加工来说有着令人信服的设计理念,解决了导致刀具系统不平衡的两个主要问题。 由于其对称性以及移动部件的缺少(如螺丝钉),它们具有固有的平衡性,径向跳动在2.5~5.0mm之间,甚至更少,并拥有回转对称的结构和小于0.003mm的圆跳动,能提供相当大的夹紧力。装夹时利用感应或热风加热使刀杆孔膨胀进行刀具的更换,然后采用风冷使刀具冷却到室温,利用刀杆孔与刀具外径的过盈配合夹紧,这种结构使刀具在高转速下仍能保持可靠的夹紧性能,特别适用于更高转速的高速铣削加工。 热缩式刀夹在实践中的表现证明,它们确实具有充足的合理性,无论高速加工还是低速加工其优势都是显而易见的。热胀冷缩紧固式刀夹的知名供应商有Kennametal、Otto Bild、Kelch(哈尔滨量具刃具集团有限公司)、Komet、Haimer等公司。 杰出人物奖 奕达精机股份有公司(以下简称“奕达”)为少数台湾本地自行开发产品及以全球营销为核心的机床制造商。2006年, 采用ERP操作系统,各产品皆通过ISO及CE验证。奕达以“精致”为公司的文化,奕达掌舵人蒲宏彦总经理被当选为荣格创新奖年度人物获胜者。 奕达的前身为杨铁机械,于2004年4月正式成立,本着人本、创新、科技的企业经营原则,以及持续产品开发、团队运作、追求永无止尽的高质量的三大坚持, 使奕达全面蜕变。 在2007年3月的TIMTOS展中,奕达展出多款车床,有BM硬铣系列、MH卧式加工中心机系列,以及新研发具双主轴带Y轴功能之车铣复合机。蒲宏彦博士表示,今年一月已获美国OEM订单约3百万美元。蒲宏彦博士认为,台湾只有制造高档次产品才能生存,奕达将以高速轻切削、高精度加工、重切削加工作为未来产品的规划方向,并积极朝向自动化及整厂输出等方向迈进; 此外,提高机床的附加价值,才能延长产品生命周期, 受客户青睐。面对市场不断的变化,满足个别客户独特的需求,奕达建立了独特的公司文化,导入管理创新,从研发、组装、售后服务,并拥有坚实的团队。蒲宏彦博士说,奕达视员工为公司最重要的资产,视员工为竞争中致胜的关键。蒲宏彦博士积极鼓励员工进修,让他们接受各种新项目,培养员工解决问题能力。一般而言,机械与电控分属两个不同的领域,奕达要求员工具备电机整合涵养,对产品相关知识要有广泛涉猎,避免有本位主义以及出现市场需求脱节现象。奕达一方面致力企业创新思维,重视员工本身的内在潜力;另一方面,建设企业文化环境,孕育“创新”的肥沃土壤。奕达的成功经验在于营造“企业文化” 。 杰出团队奖 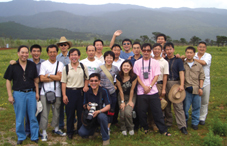 | 瑞士阿奇夏米尔集团 阿奇夏米尔国际贸易(天津)有限公司技术服务部(售后服务) | 作为以优质服务在市场竞争中获胜的阿奇夏米尔国际贸易(天津)有限公司不但给客户提供24小时专业技术服务支持和售后服务工作,并于2005年在北京设立了应用中心,这是所有机床厂家在北京设立的第一个应用中心,它的成立使阿奇夏米尔技术服务部有能力给客户提供更有效、更实际的售前及售后的应用技术支持,并对每一位客户提出的要求做出更迅捷的反应,帮助客户提高价值。具体内容包括:1. 应用工程师通过丰富的经验来协助客户进行工艺分析,推荐合适机型并制定工艺方案 ;2. 客户根据自己的要求,提供图纸或样品,在演示培训中心的机床上进行购买前试加工 ;3. 针对客户的难点工件,提供包括编程、夹具、刀具的交钥匙服务。进行不同层次的操作及应用技术培训。 |