|
深孔铰刀的改进 |
来源:信息中心 时间:2009-2-1 10:13:51 |
|
|
采用标准铰刀加工L/D>5的深孔时,操作比较困难,经常出现铰刀折断现象,且孔的表面质量不易达到加工要求,其主要原因是深孔排屑困难,堵塞在孔内的切屑容易刮伤已加工表面,并挤坏铰刀刀刃;此外,由于冷却液不易到达切削区,难以对铰刀进行有效冷却,从而加剧铰刀磨损甚至使铰刀折断。为解决这一问题,我们对标准铰刀的结构进行了改进。
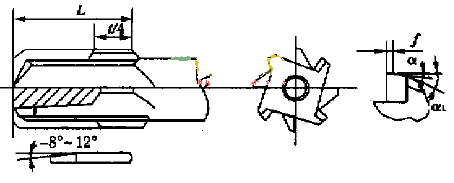 图 改进后的深孔铰刀结构 |
1 铰刀结构及特点
改进后的深孔铰刀结构如图所示。
在工具磨床上将标准铰刀的切削部分每隔一齿磨去一段,使切削齿减少一半。这样虽然加大了刀齿的平均切削负荷,但由于增大了容屑空间,使刀具排屑性能大为改善,避免了加工中切屑挤坏刀齿。此外,刀齿减少后,冷却液可顺利流入切削区,使刀具在加工过程中得到充分冷却,避免刀齿因切削温度过高而卷刃。改进后的铰刀加工寿命大大提高。据统计,一把Ø8mm 标准铰刀只能加工30余个工件即发生折断,而改进后的铰刀加工700多个工件后仍未损坏。
为避免铰刀齿数减少后对加工质量的不利影响,在磨齿时,铰刀校正部分约t/4(t为刀刃全长)处的一段刀刃仍保留原齿数。同时,在每个刀齿的切削部分磨出负刃倾角(l=-10°~-15°),以提高铰孔表面质量及铰刀寿命。
铰刀结构改进后,可提高切削速度并适当加大走刀量,使加工效率显著提高。用经改进的Ø8mm铰刀加工防爆电机机壳上92mm深孔时,铰削余量为0.3mm,机床主轴转速n=100r/min,走刀量s=0.43mm/r,冷却液为30%菜籽油+70%皂液。加工后的深孔精度可达二级,加工表面粗糙度可达Ra3.2µm。
2 铰削加工要点
- 切削速度
- 切削速度过高或过低均易产生卷屑,影响加工表面粗糙度。加工钢件时,适当的切削速度为v=4~5m/min;加工铸铁件时,适当的切削速度为v=4.5~5.5m/min。
- 铰孔余量
- 铰孔余量对铰削加工质量影响很大(对于深孔铰削尤其如此)。如铰孔余量过大,加工时铰刀易折断;如铰孔余量过小,则不能完全铰除前道工序留下的加工痕迹,影响孔的尺寸精度和表面粗糙度。根据加工经验,在钻床上进行铰削加工时,当被铰孔直径分别为3~4mm、5~10mm、12~16mm和18~30mm时,对应的铰孔余量可分别选取0.1mm、0.2mm、1mm和2mm。在车床上进行铰削加工时,铰孔余量可选取0.08~0.12mm。
- 进给量
- 根据工件材料的不同,在钻床上铰孔时,进给量可在0.17~1.5mm/r的范围内选取;在车床上铰孔时,进给量可在0.1~0.13mm/r的范围内选取。铰孔前应仔细检查机床套筒的偏摆不得过大。
- 冷却液
- 铰削加工不同材料的工件时,应采用不同类型的冷却液,如加工45钢、40Cr钢时,可采用30%菜籽油+70%皂液;加工铸铁时,只加少许煤油即可。铰孔时,冷却液的供应要充分,不能间断。
|
|
【关闭窗口】【打印该页】 |
本信息真实性未经证实,仅供您参考。未经许可,不得转载。 |
|