|
螺纹铣削技术与攻丝的对比 |
来源:信息中心 时间:2009-2-1 10:15:14 |
|
|
|
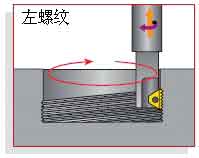 (a) |
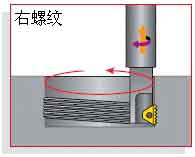 (b)
- 一把螺纹铣刀可以加工直径不同、牙型相同的螺纹。如M15x1.0、M18x1.0、M20x1.0的螺纹用一把螺纹铣刀通过改变插补半径来加工,可减少刀具数量,节省换刀时间,提高效率,方便刀具管理。
- 螺纹精度及光洁度提高。因螺纹铣削是通过刀具高速旋转、主轴插补的方式加工完成。其切削方式是铣削,切削速度高,加工出来的螺纹漂亮;而丝锥切削速度低,并且切屑长,容易损坏内孔表面。
- 内螺纹排屑方便。铣螺纹属于断屑切削,切屑短小,另外加工刀具直径比加工螺纹孔小,所以排屑通畅;而丝锥属于成型连续切削,切屑很长,并且丝锥直径和加工孔一样大,因此排屑困难。
- 可以避免丝锥反转形成的回转线(在密封要求高的情况下是不允许的)。因为加工原理不同,螺纹铣刀根本不存在回转线,而丝锥无法避免。
- 不易形成粘屑的现象。对于比较软的材料在加工过程中容易产生粘屑现象,但螺纹铣削高速旋转,并且断屑切削;而丝锥切削速度低,全螺纹与加工表面作用,容易造成粘屑。
- 要求机床功率低。因为螺纹铣削是断屑切削,刀具局部接触,受切削力小,而丝锥是全螺纹接触,作用力大,要求机床很大的功率。
- 刀具折损容易处理。首先螺纹铣刀作用力小,很少发生折损现象,如果发生了,因为加工孔径比刀具大,折断部分很容易取出;而丝锥受力大、排屑不畅,容易折断,折断后大孔处理起来稍微容易些,如果是小孔就非常麻烦,如
- 加工普通螺纹时,单纯从单件成本考虑,采用螺纹铣削并不划算。普通螺纹归类为一般硬度<50HRC、直径<38mm的螺纹,当然这不是明显的划分界限。普通丝锥一般为高速钢材料,市场价格几十块钱,然而螺纹铣刀是其价格的10倍以上,而单件寿命无法达到10倍以上。
- 长径比不能太大,一般需要L/D<3。因为螺纹铣刀单边收力,长径比太长螺纹会产生锥度,并且刀具容易折断。
两种工艺的选择
- 由于螺纹铣削是通过主轴高速旋转并螺旋插补来实现,所以如果想享受新技术的乐趣,必须配备加工中心(至少三轴联动),如果设备落后,没有加工中心,则不适合使用螺纹铣削,只能选择丝锥。而以下比较是在有加工中心的设定下进行。
- 大批量、普通硬度、一般大小的螺纹(D<38mm),很中肯的说,从经济的角度考虑,丝锥更实在。但以色列VARGUS最小螺纹铣刀目前可加工M1.6mm,技术仍在不停改进,甚至可加工更小的孔径。另外,直径大于12mm,可以采用刀片式螺纹铣刀。
- 如前所述,深孔螺纹目前更适于采用丝锥,主要因为螺纹铣刀单边受力,所加工螺孔长径比一般需小于3。
- 大直径孔的加工(D>38mm),适于采用螺纹铣削,因为螺纹铣削是局部接触,受力小,一般的机床功率就足够。而丝锥全螺纹接触,受力大,要求大功率的设备。另外从刀具的价格来讲,一只大直径的丝锥价格并不比一套螺纹铣刀低,甚至更高。而且螺纹铣刀可以选择刀片式,只要更换刀片即可,其经济性不言而喻。从各方面考虑,螺纹铣刀更适合。
- 小批量螺纹加工,也适于采用螺纹铣削。首先螺纹铣刀可以加工各种直径不同、螺纹相同的工件,因此可减少刀具数量。即使在螺纹不同的情况下,采用刀片式螺纹铣刀,只要更换刀片型号,就能加工各种各样的螺纹,无论是初期成本投入,还是使用灵活度,都是丝锥无法比拟的。
- 模具或者较大零件,适于采用螺纹铣削。在加工过程中,刀具被折断该如何处理?如果用丝锥,当然可用电火花把断枝打掉,但过程会非常复杂,另外如对零件造成损坏那就会因小失大。倘若使用螺纹铣刀,首先因为受力小,不容易断;即使断了,因为加工孔径比刀具直径大,断枝很轻易就能取出。就产品合格率而言,螺纹铣削远远高于丝锥。
- 高硬材料的加工(硬度>50HRC),适于采用螺纹铣削,因为铣削是断屑切削,局部接触刀具受力小,刀片都是硬质合金加涂层,所以磨损小、寿命长;而一般的高速钢丝锥根本无法加工,如采用整体硬质合金丝锥其价格也不菲,与螺纹铣刀价格差不多。据我们现有加工经验,螺纹铣削加工效率、经济性绝对高于丝锥。
- 复合孔(带倒角)加工同样适于采用螺纹铣削,螺纹铣刀具有多种功能,可集螺纹和倒角加工于一体。
- 薄壁加工,适于采用螺纹铣削,螺纹铣刀加工受力小,因此变形小。另外,底孔可以做成平底,螺纹可以接近底部,因此所需空间小。
- 对于螺纹精度要求较高的加工,因螺纹铣削线速度高,排屑好,螺纹精度及光洁度高,也更适于采用螺纹铣削。
- 采用螺纹铣削利于实现高效率加工,现在螺纹铣刀已发展到钻孔、倒角、锪面、螺纹多工序于一体;另外,内外螺纹、左右螺纹可用一把刀加工;可以使用多刀片刀盘;退刀迅速。
- 软材料、钛合金加工,适于采用螺纹铣削,因为螺纹铣刀不易产生粘屑现象。
- 对于不稳定切削,螺纹铣刀因其切削原理本身就是断续铣削,完全能适应这种条件的加工。
- 当然,使用者可以根据生产设备、工艺要求、精度要求、成本要求来选择适合自己的加工方式,相信螺纹铣削会逐渐被人们了解并深入生产实际。
|
|
【关闭窗口】【打印该页】 |
本信息真实性未经证实,仅供您参考。未经许可,不得转载。 |
|