|
多刃车刀改善加工表面质量的机理分析 |
来源:信息中心 时间:2009-2-1 10:23:13 |
|
|
1 引言
在车削加工中,加工表面质量通常随着切削深度的增加而降低,因此,为达到加工表面质量要求,往往不得不减小切削深度,采用多次车削来切除加工余量。多刃车刀的应用则可有效缓解加工表面质量与加工效率之间的矛盾。
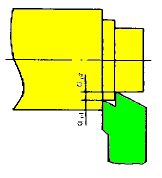 加工时,工件表层在切削热作用下产生热膨胀,而里层基体材料受温度影响较小,使表层热膨胀受到限制而产生压应力。当切削温度超过材料弹性变形范围后,表层将产生热塑性变形。切削加工结束后,温度下降,材料膨胀恢复,但表层因产生热塑性变形不能完全恢复,因此在表层塑性区产生了残余拉应力,基体材料中则产生与之平衡的压应力。切削过程中的冷塑性变形与热塑性变形产生的残余应力方向相反,可相互抵消一部分。但因切削加工中冷塑性变形较大,热塑性变形较小,所以表面残余应力总体上表现为压应力。
采用多刃车刀加工时,由于切削热不易散发,切削温度较高,因此产生的热塑性变形及引起的残余拉应力sF也相对较大,通过与冷塑性变形引起的残余压应力sB相互抵消,最终可减小工件表面残余应力s残,计算方法为
s残=sF-sB=aEDt-sB式中:a——线性膨胀系数
E——弹性模量
Dt——温升
由图3所示材料屈服强度曲线可知,TB越高,则sB越小,sF越大,故s残随温升增大较快。
 图3 温度与残余应力的关系 |
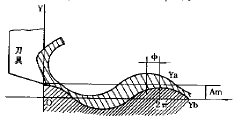 图4 刀具与工件的相对振动位移 |
表面波度
工件表面波度主要由加工系统的颤振引起。当车床径向切入加工时,若切削过程受到一个瞬时扰动,使工件与刀具产生相对振动,就会在工件表面留下一段波纹;在下一转切削时,刀具在带波纹表面切削,切削厚度的变化会引起切削力波动,这种在动态切削力作用下引起的加工激振称为再生颤振。图4所示的刀具与工件相对振动位移分别为Ya和Yb,其方程为
{ |
Ya=|Y|cos(wt+y) |
Yb=|Y|coswt |
切削厚度随时间变化的分量为
u(t)=Ya-Yb=|Y|[coswt(cosy-1)-sinwtsiny]
=-|Y|2sin(y/2)[sinwtcos(y/2)+coswtsin(y/2)]
=2|Y|sin(y/2)cos[wt+(p/2+y/2)]
由于多刃车刀每个切削刃的初相位不同(分别为y1、y2、…),因此切削厚度随时间变化的分量u(t)也各不相同,即每一时刻各个切削刃的切削厚度不同,这样就破坏了加工系统的再生颤振,从而减小加工表面波度。
多刃车刀由于具有多个切削刃,在车削加工中可减小加工表面粗糙度和表面残余应力,部分消除工件表面冷作硬化和加工系统的再生颤振,从而可有效提高被加工工件的表面质量。
|
|
【关闭窗口】【打印该页】 |
本信息真实性未经证实,仅供您参考。未经许可,不得转载。 |
|
|