|
重型车床刀具及切削用量的选择 |
来源:信息中心 时间:2009-2-1 10:50:01 |
|
|
1.引言
重型机械加工行业的特点是被加工件的尺寸很大,重量很重(有的可达上百吨),因此重型加工用卧式车床的回转直径可达到6米,立式车床更可达到10余米。与普通切削加工相比,由于重型切削加工具有切削深度大、切削速度低、进给速度慢等特点,因此其加工工艺与普通的机械切削加工工艺有很大不同,这些工艺问题包括刀具的选择、刀具的安装、切削用量的选择以及工件的装夹等各个方面。本文对重型车床切削加工不同加工阶段的特点分别作如下论述。
2.刀具的选择
机械加工中常用的刀具材料主要有高速钢、硬质合金、立方氮化硼(CBN)、陶瓷等。由于重型切削的特点(切削深度大,余量不均,表面有硬化层),刀具在粗加工阶段的磨损形式主要是磨粒磨损。由于切削温度高,尽管切削速度处于积屑瘤发生区,但高温可以使切屑与前刀面的接触部位处于液态,减小了摩擦力,抑制了积屑瘤的生成,所以刀具材料的选择应要求耐磨损、抗冲击,刀具涂层后硬度可达80HRC,具有高的抗氧化性能和抗粘结性能,因而有较高的耐磨性和抗月牙洼磨损能力。硬质合金涂层具有较低的摩擦系数,可降低切削时的切削力及切削温度,可以大大提高刀具耐用度(涂层硬质合金刀片的耐用度至少可提高1倍)等优点,但由于涂层刀片的锋利性、韧性、抗剥落和抗崩刃性能均不及未涂层刀片,故不适用高硬度材料和重载切削的粗加工。陶瓷类刀具硬度高,但抗弯强度低,冲击韧性差,不适用于余量不均的重型切削,CBN刀具同样也存在这个问题。综合以上分析,只有硬质合金刀具适合于重型切削的粗加工。硬质合金分为钨钴类(YG)、钨钴钛类(YT)和碳化钨类(YW)。加工钢料时,由于金属塑性变形大,摩擦剧烈,切削温度高,YG类硬质合金虽然强度和韧性较好,但高温硬度和高温韧性较差,因此在重型切削中很少应用。与之相比,YT类硬质合金刀具适于加工钢料,由于YT类合金具有较高的硬度和耐磨性,尤其是具有高的耐热性,抗粘结扩散能力和抗氧化能力也很好,在加工钢料时刀具磨损较小,刀具耐用度较高,因此YT类硬质合金是重型加工时较常用的刀具材料。然而在低速切削钢料时,由于切削过程不太平稳,YT类合金的韧性较差,容易产生崩刃,而且在加工一些高强度合金材料时,它的耐用度下降很快,无法满足使用要求。如电站用机械产品工作于高温、高压、高转速的环境中,对材料(如26Cr2Ni4MoV、Mn18Cr18)机械性能的要求非常高;而一些高硬度轧辊,表面硬度在淬火后可达Hs90,YT类刀具在加工此类产品时就无法胜任,在这种情况下应选用YW类刀具或细晶粒、超细晶粒合金刀具(如643等)。细晶粒合金的耐磨性好,更适用于加工冷硬铸铁类产品,效率较YW类刀具可提高一倍以上。
精加工阶段同样要求刀具耐磨损,但是精加工阶段的磨损形式是以粘蚀磨损为主,这时的切削速度虽然有了很大提高(可达到40m/r),但由于工件材质等原因,仍然会产生积屑瘤,当积屑瘤增长到一定高度时会从刀具上剥离,将接触部位的刀具材料带走一部分,形成刀具的磨损。同时,剥离的积屑瘤会扎进工件表面,形成硬点,降低加工表面质量。因此,如果精加工时仍然采用普通硬质合金刀具,则刀具磨损非常快,换刀次数增多,不仅影响加工效率,也易在工件表面形成接刀痕迹,影响外观质量。解决这个问题的办法就是改变刀具材料。在实际加工中发现涂层刀具比较适合重型切削的精加工,刀具的涂层减小了切屑与刀面间的摩擦,减少了积屑瘤的发生,降低了刀具的磨损,延长了刀具的寿命。实际加工中,我们采用瓦尔特公司的涂层硬质合金刀片,在加工45Cr4NiMoV支撑辊时,刀具耐用度提高了一倍;但使用陶瓷刀具未达到预期效果,当切削速度达到100m/min时,刀片的磨损显著加快,这是因为陶瓷刀具与金属材料之间由于亲和作用加剧了刀具的磨损。高速钢刀具在精加工阶段得到了广泛的应用,由于高速钢刀具的锋锐性较好,经常用于精加工阶段的光整工序以去除微小余量,目前来看,其它刀具还无法完全取代高速钢刀具的作用。
3.刀具角度的选择
由于在重型机械粗加工阶段刀具的工作环境比较恶劣,比如材料锻造后的氧化皮、裂纹、铲坑、铸造后的夹杂、气孔等缺陷,都易导致刀具的损坏,因此应选择适当的刀具角度。用于重型切削的刀具一般采用0°~-5°前角,10°~15°后角,采用负的刃倾角,以增大工作前角和楔角,提高刀刃的锋利性和刀尖的强度。同时,在主切削刃上开有1mm左右宽的负倒棱、R2mm左右的刀尖圆角以提高刀刃的抗冲击性能。当然,这些角度还要根据实际加工情况进行调整。
精加工阶段以保证产品精度为主要目标。刀具的锋利对切除微小的余量极为重要。这时选用的刀具角度一般为:前角10°,后角15°,刃倾角10°;当用平刃刀片精光时,前角达25°~30°,后角15°,刃倾角20°,属斜角切削。刀刃在刃磨后,应该用金刚石砂条或细目油石条进行研磨,去除微小毛刺及微裂,增强刀刃的锋锐性和强度,并用刀尺进行透光检查,保证刀刃的平直度。
4.刀具结构的选择
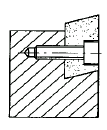 当刀块与刀体间有误差时,可以进行修磨,从而保证装配精度;压紧螺栓位于后刀面上,不容易被切屑损坏。板式刀架比较适合重型切削,因为它极大地增加了刀片受力方向的刚度,可以使得在增加切削用量后,不会产生振动,有利于生产效率和加工质量的提高。
5.刀具的安装
机械加工中刀具的安装方式对于加工很重要。通常以正夹为主,但计算结果表明,反夹的刚度更好,如
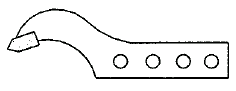 图3 弯头反切断刀 |
6.切削用量的选择
重型切削粗加工阶段的切削深度可以达到单边50mm,相应的切削速度为10m/min左右,进给量1.5mm/r。因为粗加工阶段以去除余量为主要加工目的,因此按照机械加工中切削余量的确定原则,为提高切削效率,应加大切削深度。
重型切削时由于切削深度大,所以切削力大,相应的选择较低的切削速度,一般为10~15m/min,进给量为1~2mm/r。采用这样的切削用量,工件的表面粗糙度比较差,只能达到Ra12.5~Ra6.3,可以通过滚压的方法提高粗糙度值,以满足后序加工的要求。
重型机械加工的产品尺寸较大,所以很多产品的精加工只能在重型车床上进行。精加工时切削速度较高,一般可达40~50m/min。如果机床及刀具性能允许,应尽可能提高切削速度,相应的可以采用较小的进给量,以利于表面质量的提高(一般可取0.1~0.2mm/r)。如果刀片有修光刃,则可根据修光刃的宽度,适当加大进给量。当采用光刀精光外圆表面时,进给量可以达到每转几十毫米,这时切削速度降为3m/min左右,并采用煤油进行润滑。精加工时,加工余量较小,从而切削深度也较小,对于形状精度较高的表面,应分多次去除余量,这样可以有效消除残留的形状误差,这一点对于易变形的工件尤其重要。
7.结语
重型切削同普通切削相比,其实际加工同理论计算均有很大的区别。目前,重型切削的很多工艺及刀具资料都是以普通机械加工为依据,并不完全适用于重型机械加工,因此需要进一步专门深入研究。
|
|
|
【关闭窗口】【打印该页】 |
本信息真实性未经证实,仅供您参考。未经许可,不得转载。 |
|